Supply chain : notre guide
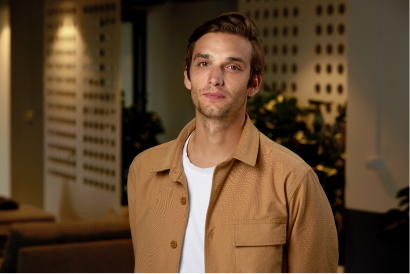
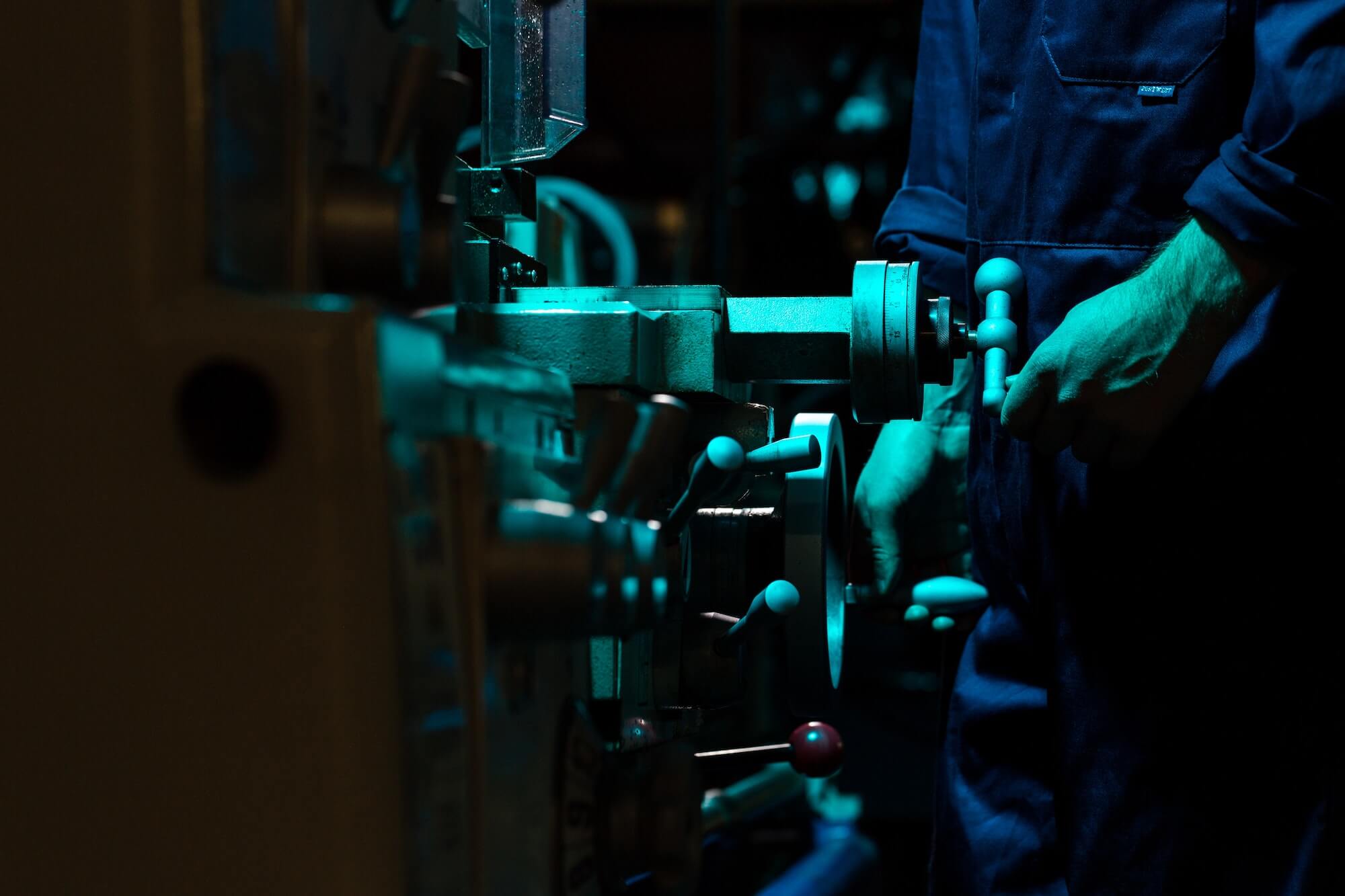
S'abonner maintenant ! Recevez 15% de réduction.
Rejoins notre newsletter et choppe -15% sur ta première commande. Promis, pas de blabla inutile.
Vous êtes maintenant inscrit!
Dans cet article :
La supply chain et sa gestion sont un vaste sujet.
Pour vous aider, nous avons décidé de nous y attaquer et de la décortiquer afin d’essayer, du mieux que nous le pouvons, de le rendre digérable et intelligible.
Pourquoi ? Pour que vous soyez en mesure de connaître tous ses aspects et ainsi optimiser votre chaîne logistique.
En effet, la supply chain est au coeur de votre organisation car par son côté transversal elle touche à tous les départements de votre entreprise : finance, IT, production et même un peu marketing.
De plus, elle touche de nombreux aspects : approvisionnement, fabrication, préparation de commande, livraison, etc.
En parlant de préparation de commande, on a dédié tout un article très complet pour vous aider à l’optimiser. Améliorez votre préparation de commande dès maintenant.
Il est donc crucial pour votre entreprise d’être à même d’optimiser sa chaîne logistique. Les enjeux sont gros : réduction des coûts, image de marque, etc.
L’image de marque ça peut passer par le respect des délais de livraison mais aussi simplement par un packaging fiable et séduisant pour vos clients !
Packhelp vous accompagne pour réaliser votre emballage sur mesure. Profitez de notre expertise et de notre réseau de fabricant pour optimiser vos coûts.
Voir ce qu’on peut faire pour vous
Bref, dans tous les cas nous reviendrons sur tout cela plus tard en détail.
Mais nous allons d’abord commencer avec les basiques comme la définition d’une supply chain.
D’ailleurs, voici ce que vous aurez appris à la fin de cet article :
- Ce qu’est la supply chain (+schéma)
- Les enjeux et finalités de la supply chain
- Optimiser votre supply chain 1 : choisir les bon KPIs
- Optimiser votre supply chain 2 : les méthodes de gestion de la chaîne logistique
Commençons donc par le commencement !
Supply chain : définition et schéma explicatif
Des définitions de la supply chain (traduction : chaîne logistique en français), il y en a de nombreuses.
Nous allons donc vous en proposer quelques unes afin que vous puissiez saisir l’essence de ce qu’est le supply chain management.
Car, lorsqu’on parle de supply chain, on parle de management.
Vous avez peur d’être perdu avec plusieurs définitions ?
C’est pour cela que nous finirons par ce qui nous paraît être la meilleure définition de la supply chain.
La supply chain et par conséquent le supply chain management (SCM) c’est la gestion des tâches et flux (matériels et d’information) qui permet de maîtriser la production et l’approvisionnement de matières et marchandises et de respecter ses engagements de délais et coûts auprès du client.
Quoiqu’un peu complexe, nous aimons beaucoup cette définition de la supply chain qui dresse un portrait précis de la gestion de la chaîne logistique (GCL).
Voici une autre définition plus abordable.
Le supply chain management (SCM) c’est la gestion de l’ensemble des ressources, moyens, outils, techniques et méthodes destinés à piloter le plus efficacement possible la chaîne d’approvisionnement et de livraison d’un produit ou d’un service jusqu’au client final.
Enfin, voici la définition de la supply chain qui est la meilleure selon nous.
La supply chain sont tous les acteurs, activités et processus qui permettent de fabriquer et distribuer un produit à un client final.
Est-ce que c’est plus clair comme cela ?
Pour rendre tout cela encore plus limpide, nous avons réalisé un schéma de la supply chain avec ses acteurs et flux :
Ce schéma résume bien les différentes étapes, flux et implications de la gestion de la chaîne logistique.
Mais il est simplifie un peu le tout pour le rendre intelligible.
En effet, il y a fréquemment plus d’étapes, notamment avec des grossistes ou centrales d’achat en plus par exemple. Mais ce n'est pas le cas si vous vendez en D2C (Direct to Consumer, soit de la vente directe)
Ou des transformations supplémentaires intervenant en amont de la fabrication ou de l’assemblage final du produit telles que la fabrication de composants depuis la matière première.
Plusieurs circuits de distribution peuvent également coexister depuis un même fabricant et être plus ou moins longs.
Pareillement, il y a bien sûr généralement plusieurs fournisseurs : un pour les composants, un pour les emballages, un pour les consommables, etc.
Comme vous le voyez sur le schéma, une supply chain, c’est beaucoup une histoire de flux.
D’ailleurs, on distingue en fait 2 types de flux selon lesquels les chaînes logistiques fonctionnent.
Les flux de la supply chain : flux tirés et flux poussés
Les 2 types de flux selon lesquels une supply chain fonctionne sont les flux tirés et flux poussés. Encore faut-il savoir qui tire ou pousse le flux.
Flux poussé
Lorsque le flux est poussé, il est en fait poussé vers le client.
Plus concrètement, on se base sur les prévisions de ventes (et donc de commandes) des clients pour planifier sa production.
Ainsi chaque élément de la chaîne d'approvisionnement, en commençant par le fournisseur de matières premières, pousse le flux de production vers l’étape suivante (son client) jusqu’au client final.
Autrement dit, la demande, basé sur les prévisions de commandes, vient de l’amont de la supply chain.
Flux tiré
Lorsque le flux est tiré, il est tiré par le client.
Dans un fonctionnement en flux tiré, la production est en fait déclenchée à chaque commande ferme passée par un client sur la supply chain.
Ainsi, lorsque le client final commande un produit, il déclenche la fabrication d’un nouveau produit auprès de la manufacture. Manufacture qui à son tour déclenchera une commande de composants. Et ainsi de suite jusqu’au fournisseur de matières premières.
Dans le cas du flux tiré, la demande vient donc de l’aval de la supply chain.
Avantages et inconvénients des flux poussés et flux tirés
Le flux poussé est relativement facile à gérer et évite plus facilement d’avoir des ruptures de stocks.
Mais le stock supplémentaire qu’il engendre est une immobilisation de trésorerie et donc moins de cash flow pour les autres opérations de l’entreprise.
Aujourd’hui les entreprises tendent vers le flux tiré.
Il demande une surveillance et une réactivité sans faille. Mais en revanche, les stocks sont minimisés et plus de trésorerie est disponible pour faire fonctionner les autres pôles de l’entreprise.
Nous vous montrerons et expliquerons un peu plus tard des méthodes de gestion en flux tirés pour vous aider à les maîtriser.
Les enjeux et finalités de la gestion de la supply chain
Chose promise, chose due ! Quels sont donc les enjeux et finalités de la gestion de la chaîne logistique ?
Les enjeux de la chaîne logistique
La supply chain doit répondre à deux principaux enjeux :
- La satisfaction des clients
- Augmenter sa compétitivité
Un bon supply chain management pour satisfaire les clients
À l’heure de la mondialisation et d’une concurrence accrue comme jamais, les différents maillons de la chaîne d'approvisionnement ont réalisé qu’une bonne gestion de la chaîne logistique participe avant tout à la satisfaction du client final.
On peut prendre l’exemple de l’aéronautique où la croissance de la demande a demandé une augmentation du rythme de la production.
Cela touche en effet chaque maillon de la chaîne, du fournisseur de matières premières jusqu’à l’entreprise qui fait l’assemblage final en passant par le fournisseur de composants.
Et il en est de même pour tous les secteurs et industries.
Si vous ne répondez pas à la demande client, si vos délais sont trop longs ou s’il y a un défaut de production par exemple, vos clients ne seront pas satisfaits.
Au final, c’est le risque de perdre des clients, vos coûts augmentent et votre image de marque est ternie (quand on vous disait que ça touchait aussi au marketing).
Un bon supply chain management pour être plus compétitif
Étant donné que le supply chain management s’occupe de l’approvisionnement et de la distribution d’un produit, il a un impact substantiel sur le prix final du produit vendu.
De façon plus générale, la bonne gestion de la supply chain participe de façon capitale à la compétitivité d’une entreprise.
En effet, cela peut, entre autres, aider une entreprise à livrer ses produits plus rapidement.
Amazon par exemple, bien qu’étant juste distributeur et non fabricant illustre très bien cela. L’entreprise de Jeff Bezos est certes douée marketing, mais que serait Amazon sans les livraisons en 1 jour ou le jour même ?
Être plus compétitif vous sert à diminuer vos coûts ou à obtenir un avantage sur vos concurrents (comme dans l’exemple de la livraison en 1 jour de Amazon).
En fait, tant en agissant sur la satisfaction client que sur la compétitivité, un bon supply chain management a plein d’autres effets positifs.
Voyons lesquels.
Les finalités de la chaîne logistique
Les entreprises cherchent généralement à travers la gestion de leur supply chain à :
- Gérer la qualité de service délivrée à ses clients et la qualité de collaboration avec ses fournisseurs
- Améliorer sa notoriété et son image de marque. En dehors de la supply chain, cela passe aussi par une identité visuelle bien travaillée.
- Réduire ses coûts pour augmenter sa marge bénéficiaire. Découvrez comment réduire le coût de votre approvisionnement en emballages.
- Assurer la sécurité des biens et personnes (éviter les violation de règles professionnelles, éviter les accidents, etc.)
- Agir et communiquer sur les tendances actuelles : développement durable, production éthique, transparence, etc. Découvrez comment Packhelp agit pour l’environnement.
Découvrir comment passer à la logistique verte
Maintenant que nous savons de quoi il en retourne lorsqu’on parle supply chain management, voyons comment vous pouvez l’optimiser.
Pour ce qui est de l’optimisation de l’approvisionnement en emballage, on a une solution clé en main pour vous : Packhelp vous accompagne dans la conception d’un emballage entièrement sur mesure et vous offre l’accès à son réseau de fabricants pour réduire vos coûts.
Envie de vous renseigner plus en détails sur ce qu’on peut faire pour vous ? Découvrez les avantages de notre accompagnement pour optimiser votre supply chain d’emballages.
Optimiser votre supply chain : choisir les bon KPIs
Toute bonne optimisation passe par la fixation d’objectifs et de moyens de les mesurer.
Il est fondamental de bien choisir vos KPIs.
Car les optimisations que vous déciderez ensuite de mettre en place, dépendent entièrement de vos indicateurs de performance clés.
Quels KPIs choisir pour votre supply chain donc ?
En fait, les indicateurs de performance sont propres à votre entreprise, donc on ne peut pas dire lesquels vous correspondent le mieux.
Mais si on vous en parle, c’est pas pour vous laisser dans le noir, mais bien pour vous aider.
Voici donc des exemples de KPIs généralement utilisés pour mesurer la performance d’une chaîne logistique.
Le taux de satisfaction des clients
C’est un indicateur majeur.
Car comme il se dit parfois, “un client mécontent, c’est dix clients de perdu”.
Surtout à l’heure d’internet et des réseaux sociaux, un mauvais avis a tôt fait de se transformer en bad buzz s’il n’est pas bien géré par votre Community Manager.
Et même sans internet, le bouche à oreille, bien que difficilement mesurable existe et participe toujours de façon importante à votre succès ou non.
Mais comment mesurer la satisfaction de vos clients ?
Avec internet c’est justement plus aisé : une fois le produit livré, envoyez un petit questionnaire ou un lien pour que votre client laisse son avis en précisant que cela met 30 secondes pour y répondre.
Même si le taux de réponse sera faible, il peut offrir, si vous avez suffisamment de clients au total, un échantillon représentatif.
En cas de mécontentement, n’oubliez pas de contacter votre client pour connaître la source de son mécontentement s’il ne l’a pas donnée. Cela vous permettra de mettre en place des actions correctives si vous repérez un dysfonctionnement.
Autrement, vous pouvez également mesurer la satisfaction client en vous penchant sur des indicateurs de performance plus précis dont on peut légitimement penser qu’ils donnent une indication de la satisfaction de vos clients.
Voici quelques exemples de KPIs qui font cela :
- DIF (Delivery In Full) : vous livrez à vos clients les quantités commandées sans rien oublier. Ici la préparation de commande est cruciale. Nous vous en disons plus dans notre article sur le fonctionnement et l’optimisation de la préparation de commande.
- DOT (Delivery On Time) : vous respectez votre délai de livraison. Cela implique un transporteur rapide mais aussi une préparation de commande efficace.
- DIFOT (Delivery In Full On Time) : vous respecter le délai de livraison et les quantités demandées.
Avant d’expédier quoique ce soit à vos clients, assurez-vous d’avoir un emballage en règle, notamment si vous envoyez à l’étranger.
Les coûts
Étant donné que les coûts qui surviennent au cours de la supply chain ont une incidence sur votre prix de vente et donc sur votre compétitivité et votre marge, il est nécessaire de les surveiller et mesurer.
Tout en gardant à l’esprit que lorsque vous optimisez un coût, vous souhaitez tout de même que ce dont vous réduisez le coût offre toujours la même qualité de service.
Quels coûts surveiller donc ?
- Coûts d’achat : pièces détachées, matières premières, équipement, emballage etc. Pour ce qui est de l’emballage, on vous conseille de jeter un oeil pour comment réduire le coût de vos emballages.
- Coûts de production : machines, électricité, main d’oeuvre, maintenance, etc.
- Coûts de distribution : transport, loyer des points de vente, etc.
Le stock
Le stock… En voilà un élément sujet à discussions et interprétations.
Quelque soit votre stratégie concernant le stock de votre supply chain, vous devrez le mesurer. Cela vous permettra de savoir si vous respectez bien votre stratégie et vous indiquera où vous en êtes.
Dans tous les cas, gardez à l’esprit qu’un stock est une avance de trésorerie. Et plus votre client met de temps à acheter chez vous et donc à payer pour une partie du stock, plus cela vous coûte cher.
Voilà pourquoi il est important de savoir :
- Votre niveau de stock
- Les taux de rotation de vos produits
- La typologie de vos stocks (matières premières, produit final, équipement, emballage, etc.)
L’idéal qu’il faut viser : pouvoir être réactif vis à vis de la demande client tout en limitant la trésorerie immobilisée (votre stock).
Vous verrez plus tard, lorsque nous évoquerons les méthodes de gestions de la chaîne logistique, que la réduction du stock fait toujours partie des objectifs de ces dernières.
Le lead time
Mais qu’est-ce que le lead time ?
C’est le temps qui passe entre le début et la fin d’un processus. Ce peut être la livraison d’un produit, sa fabrication, son conditionnement, la réponse à une demande client, etc.
À lire aussi : lead time : définition, calcul et comment l'optimiser
Vous aimeriez améliorer le lead time du conditionnement de vos produits ?
Découvrez notre boîte carton d'expédition. Solide, fiable et personnalisable, elle est munie de 2 bandes adhésives. Une pour accélérer l’emballage de vos produits et l’autre pour faciliter les retours.
DÉCOUVRIR LA BOÎTE CARTON D'EXPÉDITION
Ici, le but est clair : mesurez donc le lead time de vos différents processus et cherchez à le réduire.
Par exemple, plus vous mettez de temps à répondre à un client, plus il risque d’être mécontent, ce qui va vous coûter de l’argent.
Idem par exemple pour la production d’un produit. Plus le cycle de fabrication s’allonge, plus vous aurez besoin de fonds pour le financer. Et tant que vous n’avez pas vendu ce produit, c’est une avance de trésorerie.
Réduire vos lead time permet de réduire votre BFR, c’est-à-dire le besoin en fonds de roulement.
Connaître tous les KPIs qui peuvent vous être utiles c’est bien. Mais attention à ne pas tomber dans le piège de tout vouloir mesurer et optimiser.
Il va falloir limiter le nombre de KPIs que vous utilisez. Le K de KPI fait référence à Key, l’idée est donc de se concentrer sur le plus important, l’essentiel.
De plus, ce ne serait pas réaliste d’être le meilleur sur tous vos indicateurs de performance clés. Vous pouvez exceller dans certains, alors faites-le.
Enfin, dernière chose à garder à l’esprit : les KPIs que vous utilisez pour votre supply chain doivent être en accord avec les objectifs de votre entreprise (rentabilité, satisfaction client, positionnement, etc.)
Désormais il est temps de nous attaquer aux différents méthodes pour optimiser sur votre supply chain.
Optimiser votre chaîne logistique : les méthodes de supply chain management
Il existe plusieurs méthodes de gestion de la chaîne d'approvisionnement. Elles prennent en compte tous les aspects la supply chain :
- Pilotage des ressources de production
- Planification de la production
- Systèmes et flux d’information
- Gestion de stocks
Les méthodes de supply chain management touchent donc à tous les points de cette dernière.
En effet, les étapes et flux de la supply chain sont fortement interdépendants les uns des autres. Après tout, nous parlons bien ici de chaîne.
Ainsi, les différentes méthodes sont tantôt classées dans une étape ou un flux de la supply chain, tantôt dans un autre. C’est pourquoi nous nous garderons de les classer.
En revanche, rassurez-vous, vous saurez tout ce que vous devez savoir sur les méthodes qui vous aideront à améliorer votre supply chain une fois que vous lu tout cela.
Sans plus attendre donc, plongeons dans le vif du sujet.
MRP (Manufacturing Resources Planning)
Le MRP est né dans les années 60 aux Etats-Unis et signifiait alors Materials Requirements Planning.
L’idée ? Évaluer et calculer les besoins en matières premières et composants d’une entreprise.
Dans les années 70, il devient MRP1 et s’élargit à la gestion des capacités de production autrement appelées calcul des charges.
Enfin, vient s’y intégrer la gestion d’autres ressources de production comme les machines ou la main d’oeuvre. Il s’appelle alors MRP2 et l’acronyme signifie désormais Manufacturing Resources Planning.
En gros, le MRP actuel comprend donc :
- Les consommables : matières, composants, stock, etc.
- Les renouvelables : capacité machines, main d’oeuvre, temps, etc.
Au final cela en fait un véritable outil de calcul des besoins en composants et de capacité des ressources de production.
Pour résumer, le rôle du MRP est de planifier la production en fonction des ressources de l’entreprise (matières, composants, stock, personnel, machines, temps, etc.) par rapport à un besoin à date ou à un besoin de stock.
Les besoins que le MRP doit calculer sont de deux types :
- Les besoins indépendants : ce sont les commandes estimées des clients. Le service commercial est en charge de réaliser cette estimation.
- Les besoins dépendants : ce sont les besoins internes qui découlent des commandes des clients. Les besoins dépendants sont donc ceux en composants et matériaux nécessaires à la réalisation ou fabrication de la commande client. Ils sont calculés sur la base de la nomenclature.
Le MRP fonctionne en flux poussé, la production, basée sur des estimations de la demande client est poussée vers le client.
La nouvelle évolution du MRP : les ERP
Vous connaissez certainement le terme d’ERP (Enterprise Resource Planning) car c’est un logiciel de gestion de chaîne logistique et de ressources présent aujourd’hui dans de nombreuses entreprises.
S’il est si fondamental et utile, c’est parce qu’il prolonge et améliore le MRP.
En effet, le MRP est un système de pilotage très performant pour calculer les besoins de production, d’approvisionnement et de distribution.
Le problème ? Le MRP ne tient pas compte des contraintes de production telles que les heures de travail ou la capacité nominale des ressources de production. Voilà qui est embêtant.
L’ERP vient justement corriger cela.
L’ERP, aussi appelé Progiciel de Gestion Intégré (PGI) en français, est en mesure de calculer les besoins en approvisionnement, production et distribution, selon les différentes méthodes de pilotage de flux logistique (MRP, juste-à-temps, Lean, OPT, nous allons revenir dessus juste après) tout en intégrant les contraintes liées à la production.
L’ERP permet vraiment aux entreprises d’avoir vraiment en un seul endroit une vision de toutes leurs capacités et ressources de façon réaliste.
Choisir le bon ERP est donc un choix crucial car ce logiciel est au coeur des opérations de votre entreprise. Découvrez les enjeux de l'ERP et comment bien choisir le vôtre.
La méthode de supply chain management MRP est particulièrement adaptée aux entreprises qui fabriquent des produits faits de multiples composants comme c’est le cas de l’industrie automobile par exemple.
Vous pensez que la méthode MRP ne vous convient pas ?
Voyons la méthode juste-à-temps qui a tendance à remplacer la méthode MRP (avec celle du lean également).
Juste à temps
Le juste-à-temps (Just-In-Time en anglais), également appelé flux tendu est une méthode de d’organisation et de gestion de la production dont le but est de minimiser les stocks et en-cours de fabrication.
Cela permet une économie de coût sur les stocks qui sont une immobilisation de la trésorerie.
Pour que le système de juste-à-temps fonctionne, les différents acteurs de la chaîne logistique, fournisseur, transporteur, fabricant, distributeur, doivent être très coordonnés afin que la supply chain ne soit pas interrompue.
En effet, tout incident à un point de la chaîne peut couper le flux.
Il est à noter qu’un flux tendu peut aussi bien être un flux tiré qu’un flux poussé.
Cependant, le flux tendu est généralement associé au JAT (juste-à-temps) et donc à un flux tiré.
Et c’est là où la méthode de gestion des ressources et de la production juste-à-temps diffère grandement de la méthode MRP.
Les deux méthodes de gestion ont le même but : obtenir des gains de productivité, optimiser les coûts et réduire le stocks. Mais là où la méthode MRP fonctionne en flux poussé et base sa gestion de production sur la demande anticipée du client, la méthode juste-à-temps se base sur une commande ferme.
Dit autrement, en MRP, on pousse donc le flux vers le client, tandis qu’en juste-à-temps le flux est tiré par la demande client.
Le juste-à-temps impose des délais de fabrication et distribution très courts pour livrer le produit au client et une réactivité sans faille.
Accélérez le conditionnement de vos produits grâce à notre boîte carton d'expédition. Munie de 2 bandes adhésives, vos opérateurs la scellent en à peine quelques secondes. La deuxième bande facilite les retours à vos clients.
VOIR LA BOÎTE CARTON D'EXPÉDITION
Pour fonctionner, la méthode JAT utilise souvent la méthode Kanban.
Le Kanban garantit qu’on ne produit effectivement que lorsqu’il qu’il y a une demande, sinon c’est de la surproduction (un des 7 “mudas” ou gaspillage, nous reviendrons dessus juste après).
La méthode Kanban
La méthode Kanban est née dans les usines Toyota dans les années 50/60 grâce à l’ingénieur Taiichi Ōno.
Kanban est un mot japonais qui signifie étiquette.
Si la méthode porte le nom de Kanban, c’est justement parce qu’elle se base sur des étiquettes pour optimiser le flux de production.
Expliquée simplement, la méthode Kanban consiste à lancer la production dès qu’un lot de produits est vendu grâce à un retour d’étiquette indiquant qu’il a été vendu.
Cela veut dire que la production se limite aux produits déjà vendus. C’est pour cela que la méthode Kanban fonctionne en flux tiré.
Tout cela n’est pas assez clair ? Il n’y a rien de mieux qu’un bon vieux schéma pour comprendre facilement cette méthode.
Le principe du flux tiré et du Kanban est parfois mal compris. Il ne suffit effectivement pas de mettre en place un Kanban pour que ce soit du flux tiré et que la méthode marche bien. Par exemple si vos opérateurs se retrouvent désoeuvrés et qu’on leur indique de préparer un lot supplémentaire de produits parce que “ce serait fait”, vous dérogez au principe de la demande qui tire le flux. À la place, faites leur plutôt faire un des 5S, qui sont des principes fondamentaux du lean… Que nous allons découvrir maintenant !
Lean
La méthode lean, ou encore lean management est une méthode de gestion de la production qui cherche à réduire le surplus, le gâchis, et même plus précisément le gaspillage.
En effet, l’idée est réduire les “mudas”, mot japonais qui signifie gaspillage.
Quant au mot “lean” c’est l’anglais pour dire “maigre” ou sans “sans gras”.
Ainsi, la gestion lean est la gestion sans gaspillage, la gestion allégée ou encore la gestion au plus juste.
Une fois n’est pas coutume, l’école de gestion lean trouve ses racines au Japon chez Toyota, au sien du SPT (Système de Production de Toyota).
Tout comme la méthode de gestion MRP et juste-à-temps, on cherche à réduire les coûts, les stocks et augmenter la productivité.
La méthode lean s’attaque à l’allègement de la chaîne logistique en réduisant 7 gaspillages ou 7 mudas : la surproduction, le surstockage, les délais, les transports, les processus, les mouvements et les erreurs.
- La surproduction
La surproduction dans une supply chain peut se traduire par un surplus de produits qui, de fait, se retrouvent stockés inutilement.
Mais cela peut tout aussi bien être le développement d’un outil informatique qui est trop complexe par rapport au besoin du client.
Ou encore de concevoir une formation qui est trop longue par rapport à l’attente du client.
- Le surstockage ou stock inutile
Le surstockage peut être dû à une surproduction, à une mauvaise gestion des temps d’attente ou plus généralement à une mauvaise planification.
Le surstockage peut être constitué de produits mais aussi de factures ou dossiers en attente.
- Les temps d’attente et délais
Les temps d’attentes inutiles peuvent être par exemple un opérateur inactif si une machine tombe en panne à cause d’instructions peu précises.
Cela peut aussi être un problème de synchronisation entre deux étapes de la chaîne logistique provoquant ainsi une attente inutile entre les deux.
- Les transports et déplacements inutiles
Un transport inutile peut concerner par exemple une étape de stockage intermédiaire inutile provoquant un transport supplémentaire.
Ce déplacement ou transport n’ajoute pas de valeur au client final et provoque un risque de dégradation de la marchandise inutile.
- Les étapes et processus inutiles
Un processus ou une étape inutiles peuvent prendre bien des aspects.
Vous pouvez vous retrouver avec des contrôles ou validations en surplus et donc inutile au sein de votre supply chain. Cela ne va que freiner votre flux et vous perdrez en productivité.
Un processus inutile peut également se traduire par l’ajout d’un emballage supplémentaire inutile, cela vous coûte et si ça n’apporte pas de protection supplémentaire à votre produit, cela devient inutile.
Besoin de conseil pour choisir un emballage parfaitement adapté à vos produits ? Découvrez maintenant comment bien choisir votre emballage.
- Les mouvement inutiles des opérateurs
Un peu à l’image du transport inutile, le mouvement s’applique plutôt aux employés de votre entreprise.
Il se peut que votre préparateur de commande ait un itinéraire de picking mal optimisé qui lui fasse faire des trajets inutiles pour collecter les produits dans l’entrepôt. Découvrez comment optimiser votre préparation de commande.
Un mouvement inutile peut aussi être provoqué par un matériel qui n’est pas rangé dans un endroit optimal par rapport à son usage.
Il se peut aussi qu’une information qui devrait être disponible ne le soit pas et qu’ainsi votre opérateur doive se déplacer.
- Les erreurs, défauts et rebuts
Qu’elle soit due à un produit qui se casse à cause d’une mauvaise manipulation ou à une erreur de picking lors de la préparation de commande ou à retour produit en raison d’un emballage peu fiable, une erreur, un défaut ou un rebut induit des processus supplémentaires.
Vous voulez facilement réduire vos retours clients ? Il se peut que vos produits arrivent endommagés à cause d’un emballage qui ne protège pas assez bien.
Un emballage fiable et adapté à votre produit est la clé pour éviter de nombreux retours clients et augmenter leur insatisfaction.
Profitez de notre accompagnement pour concevoir un emballage sur mesure et accédez à notre réseau de fabricants pour réduire votre coût d’emballage.
Que ce soit une retouche à effectuer ou un retour client à gérer, cela va vous coûter du temps et de l’argent supplémentaires.
Sans compter l’effet sur votre image de marque qui se retrouve ternie.
Dans la méthode du lean, on cherche donc à s’améliorer constamment (c’est l’idée de Kaizen) et à éliminer ces 7 gaspillages.
Pour parvenir à supprimer ces gaspillages, le lean utilise plusieurs outils et méthodes que nous allons voir.
Kaizen
La méthode Kaizen s’applique au supply chain management, mais constitue plus largement une démarche d’amélioration qualité pour l’entreprise.
À l’inverse du concept plus occidental qui consiste à tout jeter et recommencer à neuf comme dans l’invention ou l’innovation, la méthode japonaise du Kaizen repose sur des petites améliorations quotidiennes et constantes.
L’avantage du Kaizen c’est que l’investissement financier qu’il requiert reste marginal.
En revanche, il demande une forte motivation des employés.
Pour que le Kaizen marche, il faut :
- Créer un programme de motivation des employés (prime ou augmentation, responsabilité, avantages, statut, etc.)
- Réorienter la culture de l’entreprise
- Impliquer le management pour la mise en place du Kaizen
- Accompagner le changement
- Mettre en place des outils et démarches tels que la roue de Deming, le TQM (Total Quality Management) et un système qui facilite les suggestions et le travail de groupe
- Standardiser les processus
SMED
SMED est une méthode qui consiste à réduire le temps de changement des séries afin de pouvoir diminuer la taille des lots fabriqués, voire ultimement, fabriquer à l’unité sans augmentation de coûts.
Pourquoi s’attaquer au temps de changement de série ? Car il comporte toute une partie d’amorçage de la fabrication et de réglages qui n’est pas productive.
Poka-Yoke (ou détrompeur)
Le Poka-Yoke, une fois n’est pas coutume, est également une invention de l’ingénieur Shigeo Shingō pour le compte de Toyota (tout comme le SMED d’ailleurs).
À quoi sert le Poka-Yoke ? Tout simplement à supprimer les erreurs.
Mais littéralement.
Le but est d’atteindre le “zéro défaut” cher à Toyota (parmi les 5 zéros que sont le zéro défaut, le zéro papier, le zéro stock, le zéro délai et le zéro panne).
Bien que complexe à mettre en place, un Poka-Yoke ou détrompeur, empêche les erreurs d’origine humaine ou mécanique de se produire.
De plus, le détrompeur permet à l’opérateur d’être concentré sur son travail sans faire de tâches inutiles pour prévenir les erreurs.
La finalité du Poka Yoke ? Éliminer totalement les contrôles qualités.
Il existe 3 types de détrompeurs :
- Le détrompeur de contact :
Ce Poka-Yoke empêche l’erreur de se produire. Pour faire simple, il s’agit par exemple de la ceinture de sécurité dans les voitures qui, non bouclée, empêche leur démarrage.
- Le détrompeur de signalement :
Ce détrompeur indique qu’une opération n’a pas été faite. Pour reprendre l’exemple de la voiture, c’est le signal sonore qui retentit lorsqu’on tente de quitter le véhicule avec les phares encore allumés.
- Le détrompeur chronologique :
Ce Poka-Yoke est une suite d’opérations obligatoires qu’on doit réaliser dans un certain ordre (chronologiquement) pour lancer une machine. C’est le cas par exemple dans les cabines des avions, lorsque le pilote doit démarrer l’engin.
Les 5S
Pour changer des autres méthode, celle des 5S a également été élaborée au sein de Toyota.
Comme on peut aisément le deviner, les 5S sont des initiales.
Mais des initiales de quoi ? Il s’agit de 5 principes (en japonais) :
- Seiri (ranger) : supprimer l'inutile
- Seiton (ordre) : situer les choses
- Seiso (nettoyage) : (faire) scintiller
- Seiketsu (propre) : standardiser les règles
- Shitsuke (éducation) : suivre et progresser
En français, les principes 5S sont souvent traduits ainsi :
- Ordonner
- Ranger
- Dépoussiérer / Découvrir des anomalies
- Rendre évident
- Être rigoureux
Ce qui, si on regarde de plus près, constitue le mot “ordre” qui permet de plus facilement retenir chaque principe.
Comme nous l'avons évoqué précédemment, si vos opérateurs se retrouvent désoeuvrés entre la fabrication de deux séries par exemple, donnez leur les 5S à faire.
Bien sûr, ce ne serait pas toujours suffisant à rendre les 5S efficaces.
Heijunka
Le Heijunka est un des piliers du lean management.
C’est une technique d’ordonnancement dont le but est d’amortir les variations des commandes clients en planifiant le travail de façon séquentielle et fractionnée.
Pour ce faire, on analyse la demande moyenne des produits.
Pour le Heijunka (ou lissage de production), un travail est efficient s’il est en flux constant : il doit être standardisé et régulier (il ne doit pas varier).
Cela permet, comme nous l’avons vu dans les principes du lean, d’éliminer les 7 mudas ou 7 gaspillages (surstockage, surproduction, délais, etc.) tout en satisfaisant la demande dans les délais.
Attaquons nous maintenant à la dernière principale méthode de gestion de la supply chain, l’OPT.
À noter que l’OPT est en réalité plus un complément qu’une méthode de supply chain management globale. Aujourd’hui c’est le lean management et le juste-à-temps qui prévalent surtout dans les entreprises.
OPT
La méthode OPT (Optimised Production Technology) est une méthode de gestion des flux de production qui cherche à identifier et éliminer les goulots d’étranglement.
Le but de la méthode OPT est de faire passer un flux tendu maximum dans la chaîne tout en supprimant les stocks inutiles.
Qu’est-ce qu’un goulot d’étranglement ?
Eh bien ce peut être une machine, un atelier ou n’importe quelle ressource de production qui n’est pas en mesure d’absorber la charge de travail qu’on lui donne dans le délai imparti.
Comment fonctionne la méthode OPT ?
Les goulots d’étranglement sont les ressources de production (machines, ateliers, etc.) qui ont la plus faible capacité de production à l’heure.
En effet, chaque ressource de production n’a pas la même vitesse de travail ni le même rendement selon le poste ou le pôle dont elle fait partie.
Si ce goulot d’étranglement n’est pas identifié, il en résultera automatiquement des stocks supplémentaires car ce goulot va freiner tout le reste de la production de part sa capacité de production relativement faible comparé aux autres.
Les autres ressources de productions seront en effet bloquées par ce goulot d’étranglement et de ce fait on sera obligé de stocker.
C’est pourquoi, une fois que le goulot d’étranglement est identifié, les autres machines et ateliers doivent adapter leur flux de production au goulot afin de ne pas générer de stocks inutiles (qui est un des “mudas” que nous avons vus).
Ainsi, la capacité de production du goulot d’étranglement détermine la taille du flux sur toute la chaîne.
Il est donc primordial de bien surveiller le goulot d’étranglement car tout retard à son niveau aura des répercussions sur le délai de fabrication ou de livraison.
Supply chain : de multiples méthodes de management, un seul but
Ah, que ferait-on si les japonais et Toyota n’étaient pas là ?
Il faut le dire, que ce soit le Kanban, les 5S et bien d’autres encore, la gestion de la chaîne logistique et son optimisation ont beaucoup progressé au fur et à mesure que le Japon progressait dans ce domaine.
S’il y a une chose qu’on peut retenir du supply chain management et des différentes méthodes et principes de gestion, c’est que la réduction du stock fait partie des éléments les plus importants.
C’est un facteur de coût important et à ce titre a de nombreuses conséquences, notamment sur votre compétitivité et vos moyens (financiers) d’agir dans les autres pôles de votre entreprise.
Mais on ne réduit pas un stock sans mettre en place une des méthodes que nous avons vues.
Si on devait choisir un deuxième aspect à optimiser dans votre supply chain, il y aurait bien sûr les délais. Que ce soit celui de réglage pour une série de production, celui de livraison au client ou encore de préparation des commandes.
Vous voulez accélérer votre préparation de commande ? Lisez notre guide de la préparation de commande.
Une partie importante de la préparation de commande c’est le conditionnement des produits. En effet, c’est le seul moment où vous avez un certain contrôle sur la livraison et l’unboxing de votre produit au bout de votre supply chain.
Pour emballer de façon sûre et rapide vos produits, nous avons créé la boîte carton d'expédition. Personnalisable et dotée de 2 bandes adhésives, elle réduit votre lead time de conditionnement et facilite les retours.
DÉCOUVRIR LA BOÎTE CARTON D'EXPÉDITION
Le packaging a d'ailleurs une importance cruciale au sein de votre supply chain. Découvrez comment Apple a optimisé le packaging de l'iPhone 12 et son effet sur sa chaîne logistique.
Au-delà de réduire vos coûts, une bonne gestion de chaîne logistique vous offre aussi une bien meilleure image de marque auprès de vos clients et participe ainsi la pérennité de votre business sur le long terme.
Si après avoir lu tout cela vous songez à passer par un prestataire logistique, on vous conseille notre article pour vous aider à choisir le bon prestataire logistique.
Dans tous les cas, on espère que vous aurez trouvé dans cet article des clés qui vous aideront à y voir plus clair et à optimiser votre supply chain management.